More info about continuous columns?
Moderator: Site Moderator
More info about continuous columns?
Does anyone know a site that has more info on continuous columns?
I just had a stroke of luck, and found a decent bit of scrap 1 1/2 and 2" copper at work in the recycle pile today, with fittings. Also some battered but working thermometers and a big bucket of copper swarf, to use for packing.
It's filthy, so is going into a fuel still, and I plan to make it a continuous one - because batch runs of fuel isn't too efficient, and the foreshots/heads problems with continuous stills obviously don't happen with fuel.
So, I've read the homedistiller.org continuous section - not much info.
My issue is that I have a goodly amount of 1 1/2, but only about enough 2" to make a regular column. I also have a piece of 2" with a center feed as required for a continuous column brazed into the side... lucky coincidence???
So anyways, either my lower half ("stripping") or upper half ("rectifying") column will have to be 1 1/2" - which will choke my column more? More vapor will be flowing through the upper half, being above the feed... but more liquid will be dripping through the bottom half.
And, how should I head this thing off... I need reflux, but a small amount compared to a drinking still. I'm only aiming for 80-90%. I figure I'll do a hybrid offset/elliptical plate design, which would allow for a large range of reflux ratios, and allow "no reflux" running.
I just had a stroke of luck, and found a decent bit of scrap 1 1/2 and 2" copper at work in the recycle pile today, with fittings. Also some battered but working thermometers and a big bucket of copper swarf, to use for packing.
It's filthy, so is going into a fuel still, and I plan to make it a continuous one - because batch runs of fuel isn't too efficient, and the foreshots/heads problems with continuous stills obviously don't happen with fuel.
So, I've read the homedistiller.org continuous section - not much info.
My issue is that I have a goodly amount of 1 1/2, but only about enough 2" to make a regular column. I also have a piece of 2" with a center feed as required for a continuous column brazed into the side... lucky coincidence???
So anyways, either my lower half ("stripping") or upper half ("rectifying") column will have to be 1 1/2" - which will choke my column more? More vapor will be flowing through the upper half, being above the feed... but more liquid will be dripping through the bottom half.
And, how should I head this thing off... I need reflux, but a small amount compared to a drinking still. I'm only aiming for 80-90%. I figure I'll do a hybrid offset/elliptical plate design, which would allow for a large range of reflux ratios, and allow "no reflux" running.
Try looking up some information on the lindsay books web site. It carries a wide variety of books on a wide variety of subjects. I bought a book on the distillation process that covers continous run columns. The books are reprints of old books, any where from 10yrs to 150yrs, so the info is good but it may not be the latest and greatest.
Furball
Furball
Fourway, that's almost exactly what I've built, minus using the wash for cooling, and I've stacked the two columns. I don't think I can get 100 gallons of wash above my 2m tall column 
I was going to mount the whole column directly on top of the steam boiler, is there any advantage to doing it the way shown?
With the column directly on top of the boiler, the water is returned to the steam boiler instead of being wasted, it looks to be more heat efficient. Extra is dumped via an overflow.
120cm top column, 80cm bottom stripping column, for a total of 2m of column. It's almost done, I'll post pics and my drawings tomorrow!

I was going to mount the whole column directly on top of the steam boiler, is there any advantage to doing it the way shown?
With the column directly on top of the boiler, the water is returned to the steam boiler instead of being wasted, it looks to be more heat efficient. Extra is dumped via an overflow.
120cm top column, 80cm bottom stripping column, for a total of 2m of column. It's almost done, I'll post pics and my drawings tomorrow!
This is true and it is one of the problems with continuous columns for beverage use. Mine is for fuel so I don't mind.
They are supposed to be great for stripping runs though, as they are faster and more heat-efficient especially if you use your wash as coolant as pictured above. Your next run gets the heads.
They are supposed to be great for stripping runs though, as they are faster and more heat-efficient especially if you use your wash as coolant as pictured above. Your next run gets the heads.
Hey, the site is back up and I can post pics of my column!!
Here they come! There's no insulation on it yet because it's still under testing and also, it makes nicer pics
Here's a pic of the whole thing... pretty tall eh? 120cm on top, 60cm below feed point. Cut it down from the original 80 to save height.
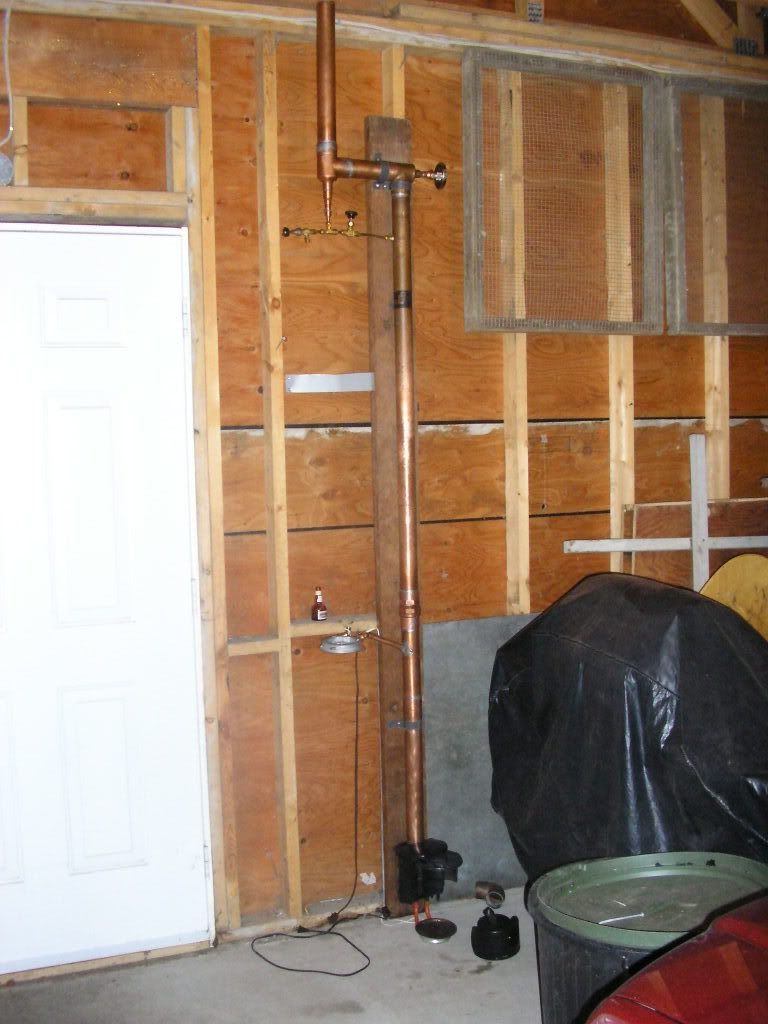
This is my offset head setup
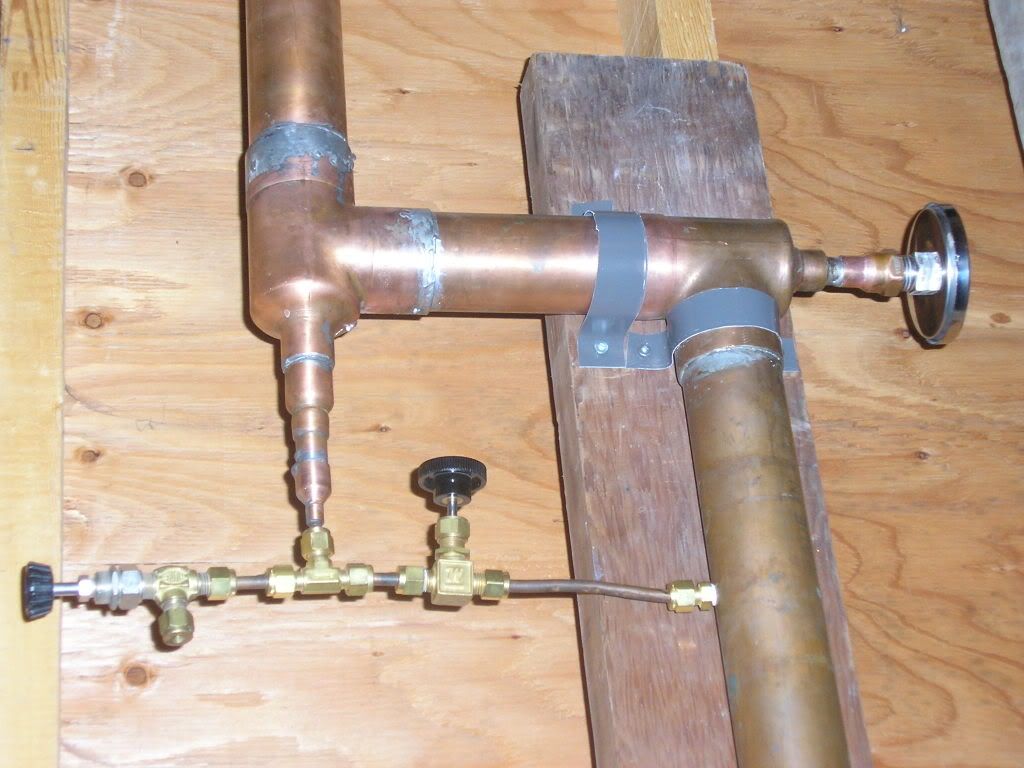
Here's the injection port with preheater. The heater came out of an old coffee maker - great as it's 900w and regulated to keep the aluminum block at ~100 degrees C - the feed ends up going in around half steam which is perfect I believe. It's only acting as an airlock right now though, as I need to wire another circuit to handle both heaters at once.
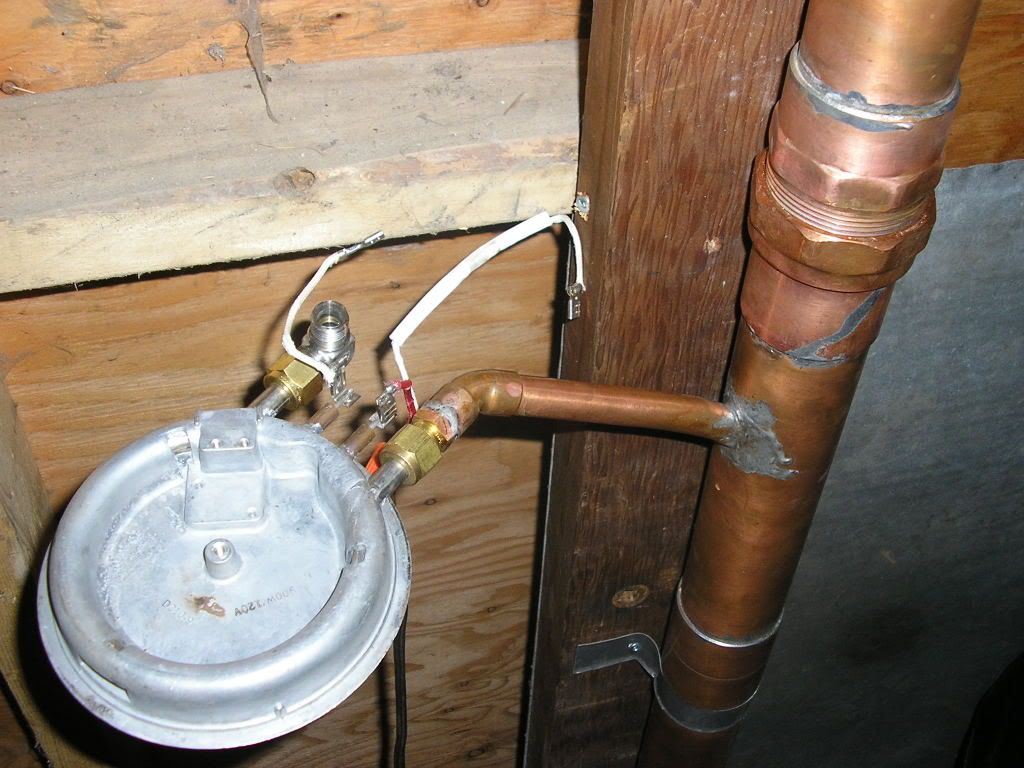
This is the boiler. Once again from an old coffee pot, 1kw this is kinda ingenious I think but a bit of an ugly prototype. Water comes down the column into that coffee reservoir, and it is hot enough to be boiled easily in the little ring heater and fired back up the column as a continuous jet of steam. Later the reservoir will be replaced by an end cap with two hose barbs for the two hoses to the ring heater, with a third higher up for drain, and the heater will be insulated to make sure all the power is going up the column.
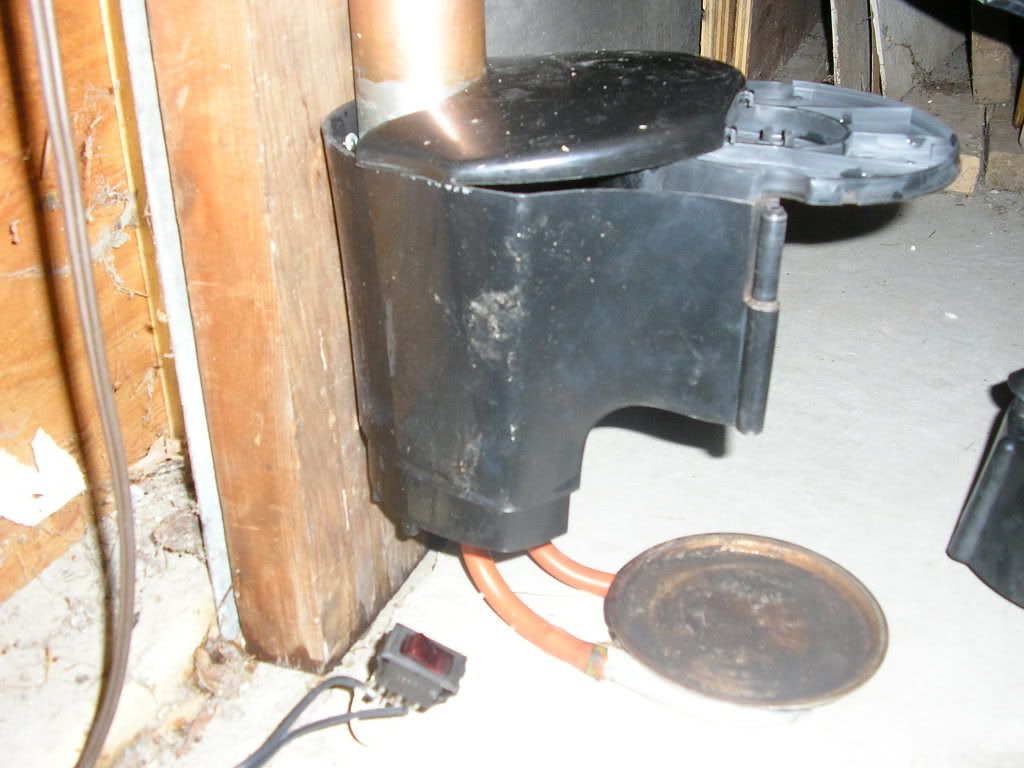
So the only bad thing at the moment, it has a crap 10' condensor which doesn't knock down all the vapors, so it operates really lossy right now. However I have a new 40' condensor waiting to be dropped in once I'm done getting caught up working on my new motorcycle... that should fix it.
In testing so far I distilled some skunky undrinkable beer at a pretty high feedrate and the column performed pretty well, even uninsulated and with the injection preheater turned off! I got some ethanol out of it, but nowhere near the 1oz you're supposed to get out of a beer. I think most got out the top because the bottom stayed at 100 C.
Here they come! There's no insulation on it yet because it's still under testing and also, it makes nicer pics

Here's a pic of the whole thing... pretty tall eh? 120cm on top, 60cm below feed point. Cut it down from the original 80 to save height.
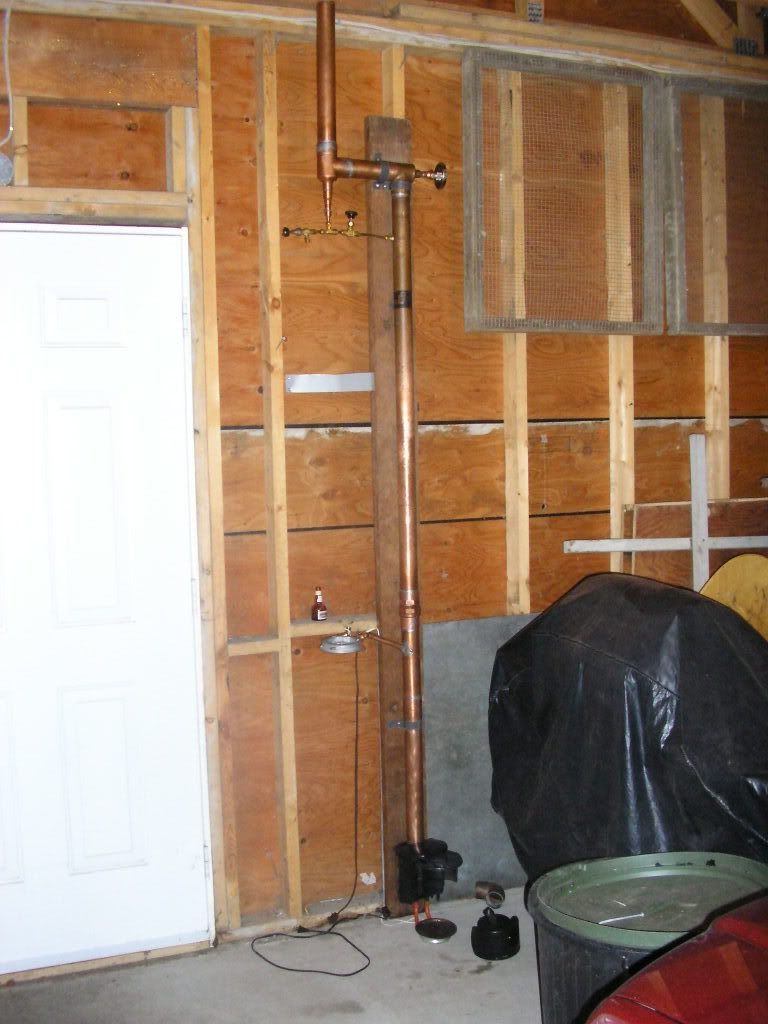
This is my offset head setup
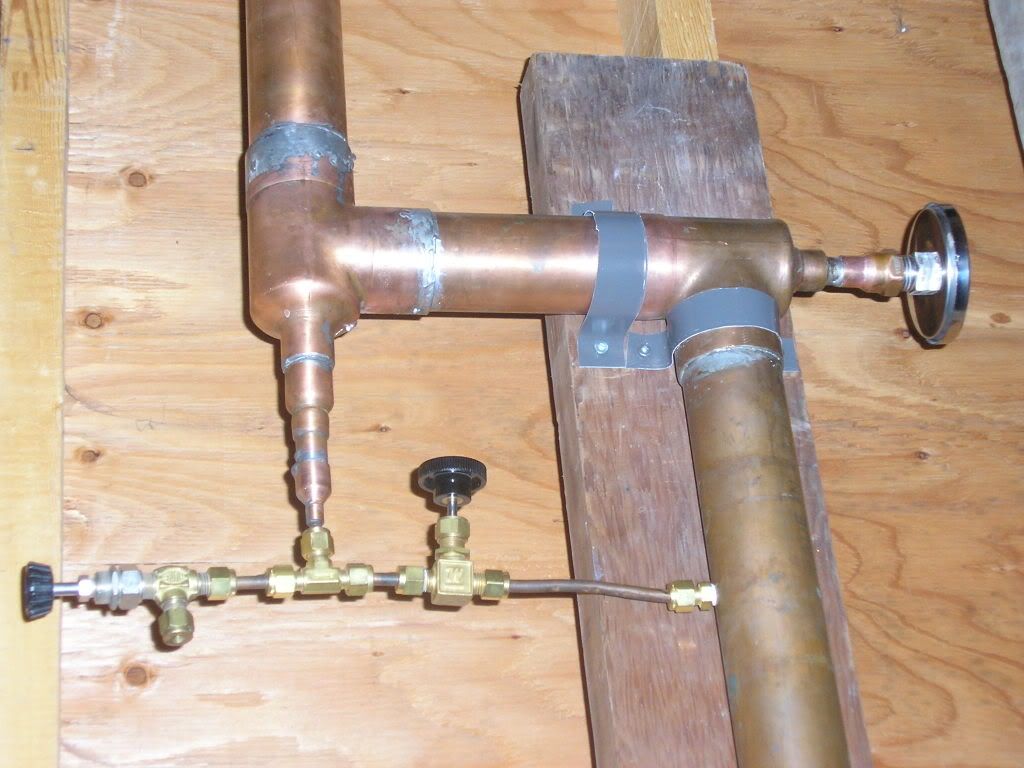
Here's the injection port with preheater. The heater came out of an old coffee maker - great as it's 900w and regulated to keep the aluminum block at ~100 degrees C - the feed ends up going in around half steam which is perfect I believe. It's only acting as an airlock right now though, as I need to wire another circuit to handle both heaters at once.
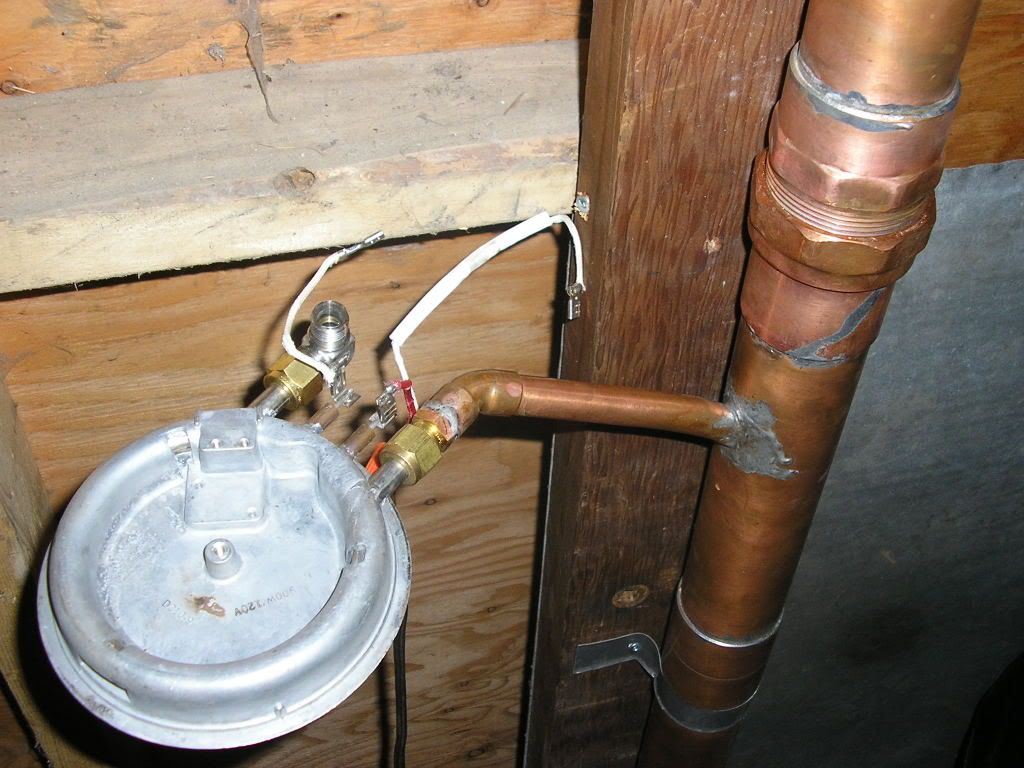
This is the boiler. Once again from an old coffee pot, 1kw this is kinda ingenious I think but a bit of an ugly prototype. Water comes down the column into that coffee reservoir, and it is hot enough to be boiled easily in the little ring heater and fired back up the column as a continuous jet of steam. Later the reservoir will be replaced by an end cap with two hose barbs for the two hoses to the ring heater, with a third higher up for drain, and the heater will be insulated to make sure all the power is going up the column.
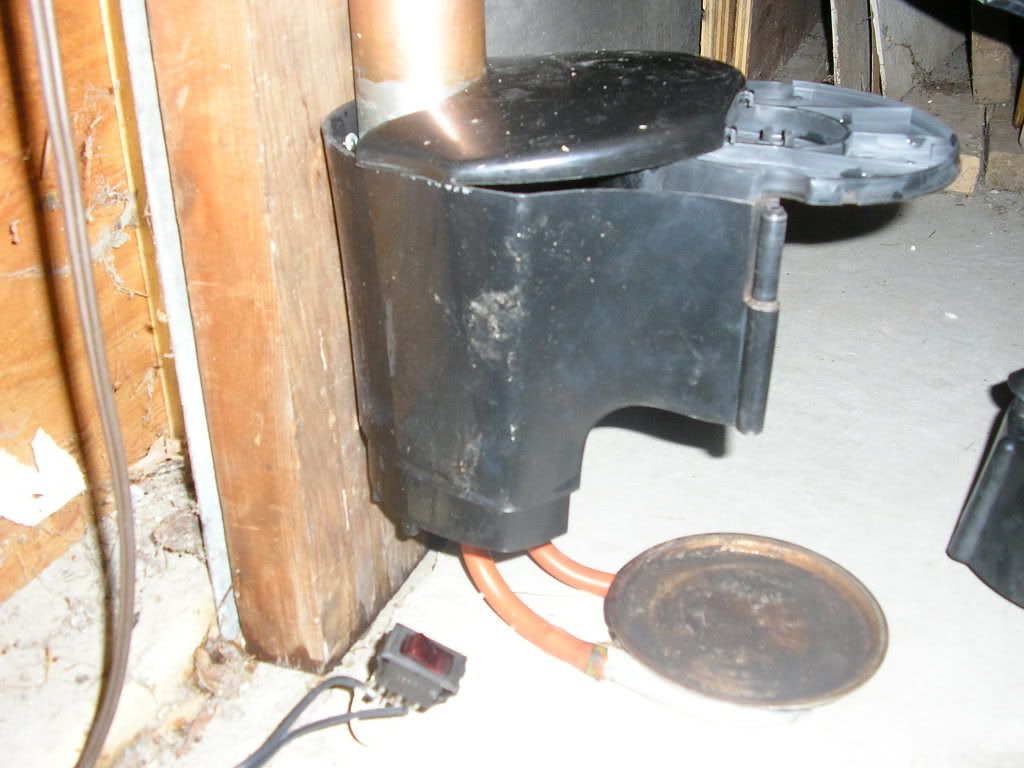
So the only bad thing at the moment, it has a crap 10' condensor which doesn't knock down all the vapors, so it operates really lossy right now. However I have a new 40' condensor waiting to be dropped in once I'm done getting caught up working on my new motorcycle... that should fix it.
In testing so far I distilled some skunky undrinkable beer at a pretty high feedrate and the column performed pretty well, even uninsulated and with the injection preheater turned off! I got some ethanol out of it, but nowhere near the 1oz you're supposed to get out of a beer. I think most got out the top because the bottom stayed at 100 C.
I like the theory behind these and i guess im going to try to build one, i use a pot still for my drinking spirits and this one will be for automotive fuels (no heads n tails problems). only problem for me is getting the larger sized copper tubing, here in the uk we just dont have it unless u want to pay $400 for a length of copper drain pipe so im looking to use some stainless exhaust pipe with copper scrubbers and copper parts where ever i can get them to fit if thisf is important when im not drinking the stuff and if i decided to drink it id run it through the pot to cut the heads n tails, for the boiler ill simply use a stainless 3 kw hidden element kettle or put an element in a cheap stockpot. is the preheating of the mash really needed?
Copper is mainly for flavor - it doesn't really matter for fuel. Reduces sulphate levels mainly - perhaps using stainless will make your exhaust smell kinda farty? Maybe hurt your cat converter a bit? I really have no idea.
I built mine from copper since it's built for free from scrap. I highly recommend using scrap or used pipe for your fuel still as it's so much cheaper and your engine doesn't care about a little bit of potentially toxic junk.
Preheat is not technically neccesary. However if you introduce your wash at its boiling point, you boost the efficiency of the whole thing and can run a higher feed rate without worrying about losing ethanol out the bottom.
I built mine from copper since it's built for free from scrap. I highly recommend using scrap or used pipe for your fuel still as it's so much cheaper and your engine doesn't care about a little bit of potentially toxic junk.
Preheat is not technically neccesary. However if you introduce your wash at its boiling point, you boost the efficiency of the whole thing and can run a higher feed rate without worrying about losing ethanol out the bottom.
Has anyone considered?
I love the idea of a cheap continuous still made from a coffee maker. Kudo's for making it work!
Has anyone considered whipping up a nice compact version of something like this for newbies to practice distilling? Something that you could pour a bottle of wine into, and double the alcohol percentage on the output?
You could even use the coffee machine water tank as a primary condensor, which in turn would pre-heat the feed to some extent.
Such a still could probably be used safely indoors, made from 1/2" copper, and sealed up with Silicon RTV. Anyone with a Dremel could make it in half an hour for under $30.
It would face problems with head/tail separation, but no more so than the bottle of wine that you put into it.
Has anyone considered whipping up a nice compact version of something like this for newbies to practice distilling? Something that you could pour a bottle of wine into, and double the alcohol percentage on the output?
You could even use the coffee machine water tank as a primary condensor, which in turn would pre-heat the feed to some extent.
Such a still could probably be used safely indoors, made from 1/2" copper, and sealed up with Silicon RTV. Anyone with a Dremel could make it in half an hour for under $30.
It would face problems with head/tail separation, but no more so than the bottle of wine that you put into it.
ok i know its nothing new but i found this diagram on the net and adapted the design as u see it on the left to the 2 ideas on the right, in theory converting to a still which will work just with gravity whereas the previous design requires some pumping, this could also be easily made from sheet stainless,, what do u think.


The first guest was, as you could probably guess, me.
2nd guest: There are problems with using a coffeemaker as a potstill which as far as I see make it completely infeasible.
Pretty much, depending on power input, flow rate, wash temperature etc, the coffee heater can act as 0-1 HETP. Now to get that 1 plate you have to get all those parameters balanced such that it is putting out vapor that contains as much ethanol as the vapor coming off a pot would.
Too fast of a feed/too low power/too cold wash, all that comes out is hot wash liquid. Too slow of a feed etc, all that comes out is steam with the same composition as the wash. 0 HETP. Get it between those, you are getting some and a lot of ethanol is staying in the liquid - start recycling the liquid and the wash temp goes up pushing you towards 0 HETP again. You see what I'm getting at here - using this thing efficiently would be much more complex than a pot and not what a newbie wants.
On the other hand it's great on the base of the column because it can recycle that ~100 deg hot water to pure steam very easily and constantly - and it's great on the injection port because all that really matters is getting the wash up around its boiling point so the column can do its work.
Brett: your design on the left is the same as my column, except in mine pipe 3 leads to the coffee heater and pipe 2 comes back from it. That liquid is hot, throwing it away instead of reboiling it is a waste of power. Of course you need an overflow too so the column doesn't fill up. Essentially it's just a much smaller, more efficient version of the boiler on the right hand side.
Also, you're running the wash through a condenser to provide reflux? Sounds good but as everyone says here I wouldn't run that condenser all the way down your rectifying column, as it'll both produce a hell of a lot of reflux and also make your gradient not as nice.
Don't know how a square column would perform but I do know that making plates is much harder to get working right than a packed column unless you are going for HUGE capacity. Remember those are not just plates with holes they are bubble cap plates and a lot of work to make. I would go with a packed pipe myself.
2nd guest: There are problems with using a coffeemaker as a potstill which as far as I see make it completely infeasible.
Pretty much, depending on power input, flow rate, wash temperature etc, the coffee heater can act as 0-1 HETP. Now to get that 1 plate you have to get all those parameters balanced such that it is putting out vapor that contains as much ethanol as the vapor coming off a pot would.
Too fast of a feed/too low power/too cold wash, all that comes out is hot wash liquid. Too slow of a feed etc, all that comes out is steam with the same composition as the wash. 0 HETP. Get it between those, you are getting some and a lot of ethanol is staying in the liquid - start recycling the liquid and the wash temp goes up pushing you towards 0 HETP again. You see what I'm getting at here - using this thing efficiently would be much more complex than a pot and not what a newbie wants.
On the other hand it's great on the base of the column because it can recycle that ~100 deg hot water to pure steam very easily and constantly - and it's great on the injection port because all that really matters is getting the wash up around its boiling point so the column can do its work.
Brett: your design on the left is the same as my column, except in mine pipe 3 leads to the coffee heater and pipe 2 comes back from it. That liquid is hot, throwing it away instead of reboiling it is a waste of power. Of course you need an overflow too so the column doesn't fill up. Essentially it's just a much smaller, more efficient version of the boiler on the right hand side.
Also, you're running the wash through a condenser to provide reflux? Sounds good but as everyone says here I wouldn't run that condenser all the way down your rectifying column, as it'll both produce a hell of a lot of reflux and also make your gradient not as nice.
Don't know how a square column would perform but I do know that making plates is much harder to get working right than a packed column unless you are going for HUGE capacity. Remember those are not just plates with holes they are bubble cap plates and a lot of work to make. I would go with a packed pipe myself.