Scrapped beer Keg from a local micro brewery, 2" copper column 24" tall, packed with mesh about 2/3 full. Condenser is 48" of 3/4" copper with a 2"PVC jacket, 1/2" water inlets/outlet driven by a 80 GPH pond pump. The barrel I will circulate water from is 25 gallons
In this first pic, The flange the column is attached to is home made. I couldn't find a flange that would fit for a pirce in my range, so I made one. Let me tell ya, when you get into 1/4" thick copper plate, it gets expensive.
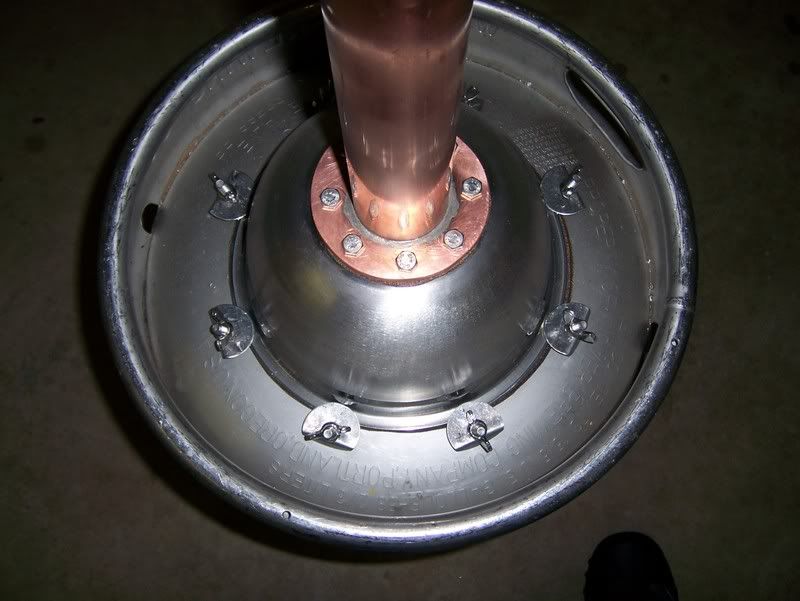
The top end assembly
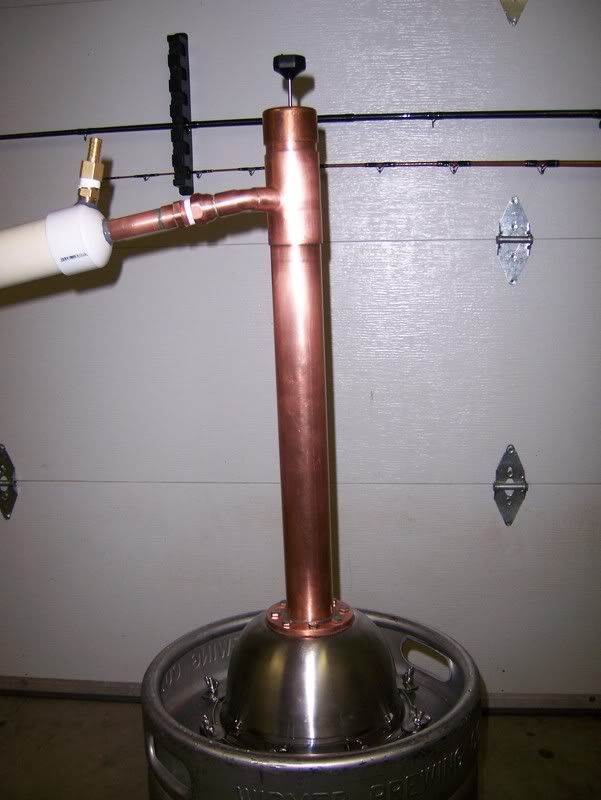
Close up of the condenser
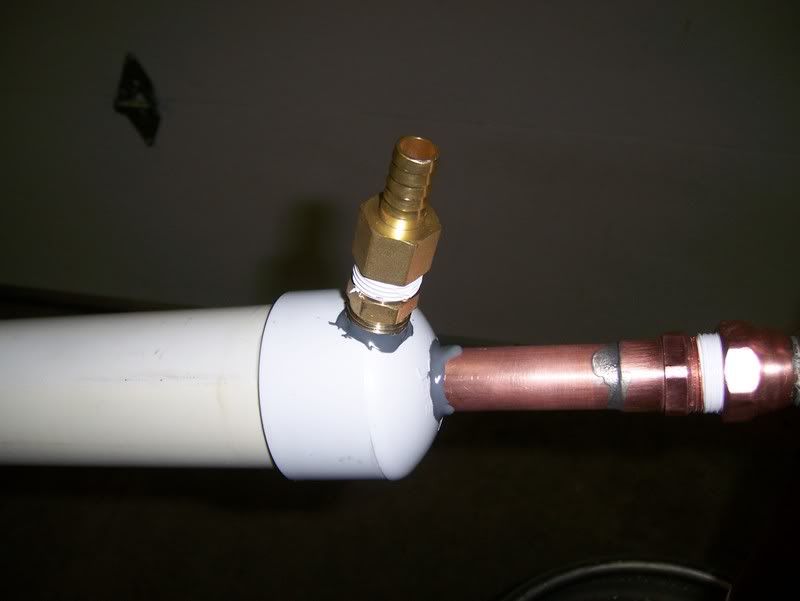
The whole thing. Already ran about 15 gallons of water thru it, fixed the three leaks I found. cleaned it paying extra attention to all the joints.
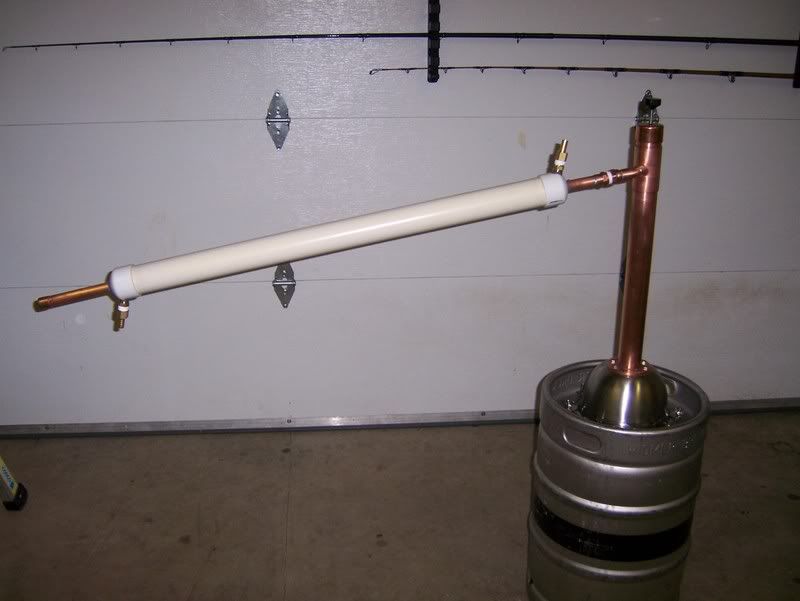
12 gallon rum wash started yesterday. Hopefully it will be done next week so I can run it
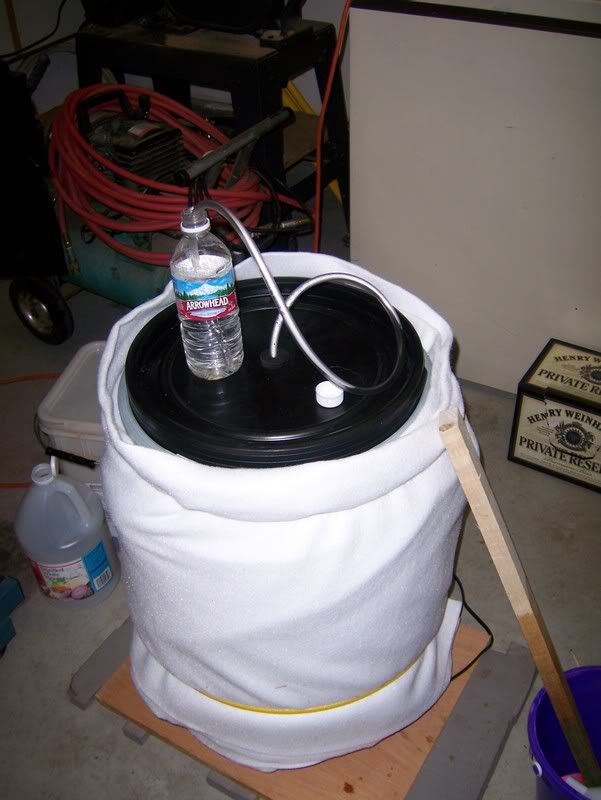
And while I was at it....decide to build one of these......
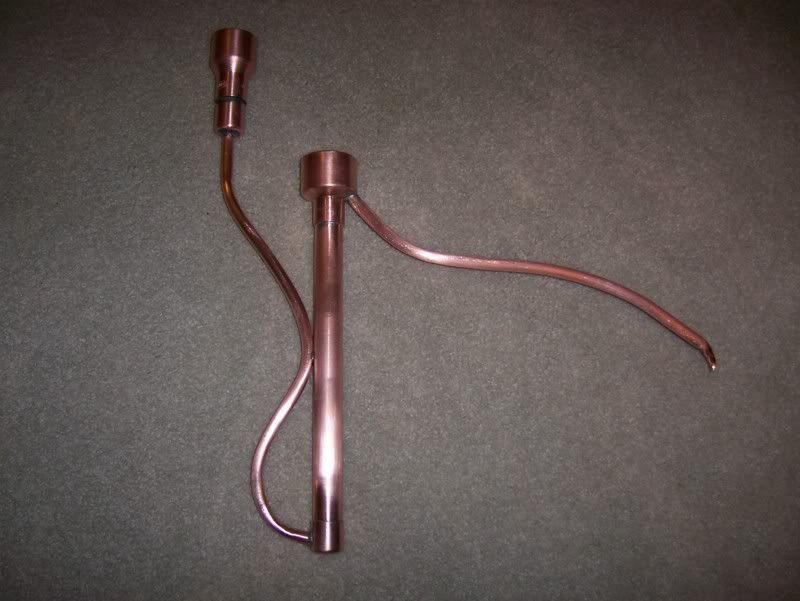
I would appreciate any comments, good or bad. Gotta learn somehow