Doug's continuous distillation
Moderator: Site Moderator
-
- Swill Maker
- Posts: 331
- Joined: Fri Feb 15, 2019 5:52 am
Re: Doug's continuous distillation
LWTSC,
Instead of additional plates you can also add a second column, right, like in your picture.
At the end there is always a "Beer column effluent" where you can measure either 1%abv or 0.1%abv or less. It depends for example on the length of the beer column, i.e. the number of plates.
Of course with a noncontinuous system you also don't get a high recovery rate for free: You have to distill longer.
My post you quoted was not meant to speak against the recovery efficiency of a continuous system, it was meant that also there a high recovery rate is not for free. And that you can have those rates also with an noncontinuous system, also not for free of course.
If it makes sense to recover more than 99.5% of the ethanol may differ from case to case.
Instead of additional plates you can also add a second column, right, like in your picture.
At the end there is always a "Beer column effluent" where you can measure either 1%abv or 0.1%abv or less. It depends for example on the length of the beer column, i.e. the number of plates.
Of course with a noncontinuous system you also don't get a high recovery rate for free: You have to distill longer.
My post you quoted was not meant to speak against the recovery efficiency of a continuous system, it was meant that also there a high recovery rate is not for free. And that you can have those rates also with an noncontinuous system, also not for free of course.
If it makes sense to recover more than 99.5% of the ethanol may differ from case to case.
Re: Doug's continuous distillation
Ah, for sure.
That's why this system (diagram) has a dedicated cooling circuit for several of the HXs.
The heat needed to maintain optimal collection speeds would otherwise overwhelm the finish distillate HX.
Using beer as the sole cooling media is not not doable if processing speed matters.
Distillation is a resource suck.
Efficiency is a nebulous priority here at the hobby scale.
That's why this system (diagram) has a dedicated cooling circuit for several of the HXs.
The heat needed to maintain optimal collection speeds would otherwise overwhelm the finish distillate HX.
Using beer as the sole cooling media is not not doable if processing speed matters.
Distillation is a resource suck.
Efficiency is a nebulous priority here at the hobby scale.
Trample the injured and hurdle the dead.
-
- Swill Maker
- Posts: 331
- Joined: Fri Feb 15, 2019 5:52 am
Re: Doug's continuous distillation
Excuse me, I don't know what HX means.
Efficiency can mean different things. For example low as possible outgoings per liter pure alcohol. But then it depends on the current and predicted costs for energy, grain, workers, taxes, steel, copper and so on how to achieve it.
Efficiency can mean different things. For example low as possible outgoings per liter pure alcohol. But then it depends on the current and predicted costs for energy, grain, workers, taxes, steel, copper and so on how to achieve it.
Re: Doug's continuous distillation
HX = Heat Exchanger
In most instances, (notwithstanding the hobby community) labor costs will almost always outweigh equipment costs over the service life of the equipment.
Therefore one could say that with respect distilling spirits, the dearest cost (notwithstanding marketing) is labor and the associated carrying costs.
In most instances, (notwithstanding the hobby community) labor costs will almost always outweigh equipment costs over the service life of the equipment.
Therefore one could say that with respect distilling spirits, the dearest cost (notwithstanding marketing) is labor and the associated carrying costs.
Trample the injured and hurdle the dead.
-
- Rumrunner
- Posts: 694
- Joined: Wed Mar 11, 2009 9:13 pm
Re: Doug's continuous distillation
On this site I have been chastised repeatedly for even alluding to commercial operations. I'd really prefer this thread not reference commercial or large volume stills.LWTCS wrote: ↑Fri Feb 18, 2022 12:23 pm HX = Heat Exchanger
In most instances, (notwithstanding the hobby community) labor costs will almost always outweigh equipment costs over the service life of the equipment.
Therefore one could say that with respect distilling spirits, the dearest cost (notwithstanding marketing) is labor and the associated carrying costs.
For hobby, I'd think time, heat costs, and wasted etoh would issues of efficiency.
2 gallons of etoh per hour.
All the etoh except under 1 percent.
2000 watt hours per gallon of etoh.
Free labor !!!
Now I know how you claim azeo so easy, it's based on a meat thermometer. :lol:
-
- Novice
- Posts: 27
- Joined: Sat Jul 18, 2020 3:58 pm
Re: Doug's continuous distillation
This is incredible! I'm so interested. I spent months reading everything I could find about small scale ethanol production after the book "Alcohol can be a gas" really captured my imagination. I'm new to this so want to learn from the established experst who are already making it work, and it really seemed like at the small scale everyone was sticking with batch runs, and in the book he even says continuous is more efficient but not possible at less than industrial scales.
But the speed and efficiency results you achieved totally disproved that. I'm super interested. It seems the website shown on the youtube video is down now, i was able to look at an old version on internet archive. It seems like at one point you were selling them as a kit? any chance you're still doing that or would consider selling plans? id love to learn more about small scale continuous distilling.
But the speed and efficiency results you achieved totally disproved that. I'm super interested. It seems the website shown on the youtube video is down now, i was able to look at an old version on internet archive. It seems like at one point you were selling them as a kit? any chance you're still doing that or would consider selling plans? id love to learn more about small scale continuous distilling.
Re: Doug's continuous distillation
The "delta-T " is NOT energy, and not proportional to energy when you change phase from liquid to gas.LWTCS wrote: ↑Thu Feb 10, 2022 4:34 pm You could use a part of the wasted energy to preheat the wash. But this won't help much, because it needs much less energy to heat the wash to its boiling point than to vaporize it.
Help much?
Mate, 10% wash will make vapor at about 190 F (88C).
If you can recover enough heat to get beer injection temps to 172F (for example) from some ambient room temp at any given location, that's not nothing. That is a huge contribution to reduce the temp split (delta t).
We're talking about a savings of (help me out here stevea) 100,000 btu/h on a system that can produce 4 barrels of finished product per shift ( for example ).
Pre-heating wash helps, but it's not huge. It's a small fraction of the still energy I used to be more tolerant of "English"/US units, but this quickly gets insanely difficult. No offense - but I'm posting in something like SI units not boiler-horsepower per firkin of wash.
To see how much energy distillation requires we need to consider the reflux ratio.
Also the MINIMUM reflux ratio acts an a lower bound.
Lets examine a (partially constructed) McCabe-Thiele diagram for a 10% ABV wash, and azeotropic distillate.
The x-axis is the liquid MOL-FRACTION, the -axis is the vapor MOL-FRACTION (mf).
The blue line is the VLE curve; the vapor mf at equilibrium w/ the liquid mf.
For example the blue line has a point around [0.1, 0.43]. This means if the liquid on a plate of 0.1mf (about 27%ABV) then the vapor above is ~ 0.43mf (about 73% ABV).
The red 45 degree line represents x = y, but also has relevance to the FULL REFLUX condition.
Notes:
A 10% wash has ~3.2% EtOH molecules, and 96.8% water molecules. So the MOL FRACTION is 0.032mf.
btw a mol of H2O is ~18 grams and 18ml
A ml of EtOH is about 46 gram and 57ml
Azeotrope is ~0.895 mf
We won't worry about the'bottoms' (waste ABV).
The Yellow q-line is very important for understanding McCabe-Thiele and also for understanding reflux requirements.
The q-line is drawn from the wash mol fraction on the diagonal (0.03, 0.03) in this case) at a slpe of (q/(q-1))
q is the quality and is defined as:
q = (energy to convert 1 mol of feed to saturated vapor at dew point) / (molar heat of vaporization)
Specific heat of water is ~75.3 J/mol.K [it takes 75 Joule to rais ethe temp of a mol of water 1 degree C(or K).
Specific heat of EtOH is ~118.4 J/mol.K
Molar heat of vaporization of H2O is ~40650 J/mol
Molar heat of vaporization of EtOH is ~38560 J/mol. (**note McCabe-Thiele assumes the molar heat of vap is about the same))
If you do the linear linear approximation ...
Specific heat of 10%ABV wash ~76.7 J/mol.K, and Molar heat o' vap of wash is 40583.
Wash values are so close to the H2O values that the difference doesn't matter!
The 'q' for liquid-phase 10%ABV wash is basically (energy to heat it to boiling + energy to vaporize ) / (energy to vaporize)
where the energy to vaporize a mol is 40583 Joule.
*IF* we need to heat the wash from ambient by 80C, energy to heat 1 mol by 80C is 80*76.7 = 6136 J, so
q = (6136+40583)/40583 = 1.15, and the slope (q/(q-1)) is about 7.5.
The example shows if we heat the wash to ~12C below the boiling point, so the yellow line tilts to the right. It would ilt a little more if we had ambient wash. If we got the wash fully to the boiling point the yellow line would be vertical.
To calculate the MINIMUM number of theoretical plates, we'd assume that we have complete reflux; *ALL the vapor is condensed and sent back down - there is no product. In that case the "operating line" (a line that represents the reflux amount) is drawn through the distillate point [0.895, 0.895] at a slope equal to the fraction of the vapor that is refluxed. At complete reflux, the slope is 1 (100% is refluxed) and to the full-reflux operating line coincide with the red diagonal. Then we must stair-step off the number of plates to reach from the 'bottoms" level (not show but perhaps x = 0.0016 or 0.5% ABV loss) up to the distillate level x= 0.895 *between* the operating line(s) and the VLE curve. Minimum plates isn't actually very interesting since there is no product at full reflux, and it uses energy.
So consider if we reduce the reflux and take some product, aka distillate off (yeah). This creates a new operating line for the rectification section, and another for the stripping section. The brown line shows an operating line where 81% of vapor is refluxed and 19% is taken off as product. The slope is 0.81. We should draw another stripper operating line from intersection of the operating line and q-line to the bottoms point {from [0.035, 0.19] to [0.0016, 0.0016] }. Now when we stair-step off the plates between these new operating lines and the blue VLE line, we will get a LOT more plates. **NOTE, whenever we reduce reflux, we get more product per unit energy, BUT it requires in more plates to get the same product.
Sadly. even with an infinite number of plates substantial reflux is required. The Green line is the MINIMUM REFLUX line, at ~0.74 slope. It intersects the Q-line at the VLE curve, so we'd need to step off an infinite number of plates to make it work. This means that even if we had a vast number of plates, we'd still need to reflux 74+% of vapor.
The 81% of vapor refluxed comes from a recommended reduction in reflux for practical still design.
===
The energy implications are this. Nearly all the energy is involved in vaporization at the base of a still or condensation at the top. Heating the wash from ambient is a relatively small matter. To make azeotrope requires refluxing a minimum 74+% of vapor, and practically 80+% of vapor. For every mol of product collected ~4 mols must be refluxed, thus costing energy.
1 liter of azeotrope is about 19 mols, and each mol costs about 40000 J to vaporize or condense.
1 l azeo => 760 kJ = 210 W hr.
But for every liter collected another (0.81 / 0.19 = ) ~4.26 l must be refluxed, so the energy for 1l of azeo product is ! 210 W hr * 5.26 = 1110 W-hr/1l azeo.
We *might* get 1l of azeo from ~9.5 liters of 10%ABV wash = 2.5 gal.
So the energy cost is, once again, 1110 W / 2.5 gal wash = 444 W-hr per gallon of wash.
====
Several comments:
a) The trade offs between reflux, more plates and energy is a tricky one, that is difficult to grasp intuitively. The thing to understand is that for a a given feed, feed-quality, and target product concentration, a majority of the energy is baked into the process.
b) Pre-heating the feed, and even heating to a partial vapor state are really good and positive ways to use waste-heat. They only modestly improve the column operation parameters. Using cold feed in the vapor condenser HX *seems* like a best-use for small scale.
c) I know many here are interested in fuel or neutral beverage production, but I have to say that whisk[e]y, at ~0.35mf vapor using the left one-third of the VLE curve admits simper stills and much lower energy costs.
d) Note that "reflux ratio" (RR) is defined as the ratio of reflux return to distillate taken off a product (L/D). Full reflux is infinite RR. But this term is awkward. The slope of the operating line is L/(L+D) (reflux to ttoal condensate) and this seems more intuitive to me.
e) Steam injection as a form of heating introduces a dilution, an therefore somewhat more costly separation. The energy calculations are complex.
f) Very substantial amounts of energy can be saved by using a heat-pump that cools the (77.5C) vapor while heating the ~100C bottom reboiler. Such hardware is likely impractical at small scale.
-
- Novice
- Posts: 27
- Joined: Sat Jul 18, 2020 3:58 pm
Re: Doug's continuous distillation
The still in this thread operates at 20 gph of 10% wash with 3800 watts, or 2000 watt hours for 1 gallon of ethanol, so 200 W-hr per gallon of wash.
There doesn't look like theres heat pumps just direct heat exchangers, and it looks like it loses heat to the environment, so its not a theoretically perfect distiller. Where could the discrepancy be

Vaporization requires heat put into the device, condensation requires heat taken from the device.
Reflux is vaporization and condensation occuring together inside the still, right? It doesn't require 38560 - 40650 J/mol coming in from the boiler for every reflux reaction?
What actually costs energy? Heat coming off uninsulated equipment into the environment. Heat in the collected product or low ABV waste being drained if those temps are above the incoming beer temperature. Heat in any external cooling beyond using the incoming feed.
So reflux cost energy because it reduces rate of product take off, so for the same quantity of product collect, it increases amount of time the equipment is operating hot and radiating heat losses into the environment.



Re: Doug's continuous distillation
I feel certain there is some measurement error.
It could be he's not getting azeotrope, nor even neutral spirits (US Fed definition 95%ABV). [that's not enough to explain it ...]
It could be the power in isn't correctly measured. [** my guess]
It might even be that there is some crazy re-compression and energy transfer [not nearly enough to explain his results].
I'm definitely NOT calling anyone dishonest. We all make mistakes [see my next post]. But the OPs claim violates basic ChemE calculation & theory established almost a century old and widely used. It's not off by a few percent, it's about half the ideal limiting value. It's a safe bet this claim is wrong in some way.
>> Vaporization requires heat put into the device, condensation requires heat taken from the devicefootball29 wrote: ↑Tue Mar 15, 2022 10:49 am [
Vaporization requires heat put into the device, condensation requires heat taken from the device.
Reflux is vaporization and condensation occuring together inside the still, right? It doesn't require 38560 - 40650 J/mol coming in from the boiler for every reflux reaction?
What actually costs energy? Heat coming off uninsulated equipment into the environment. Heat in the collected product or low ABV waste being drained if those temps are above the incoming beer temperature. Heat in any external cooling beyond using the incoming feed.
So reflux cost energy because it reduces rate of product take off, so for the same quantity of product collect, it increases amount of time the equipment is operating hot and radiating heat losses into the environment.![]()
![]()
![]()
And LOTS of it. Vaporization& condensation are huge energy(enthalpy) uses.
>> Reflux is vaporization and condensation occurring together inside the still, right?
Yes. There is pure vaporization at the reboiler at the bottom of a column still. There is pure condensation at the top.
At every PLATE there is 'absorption' where the energy of the vapor from below, mixes with the liquor on that plate, and energy added from below produces (roughly) the same molar amount of vapor above; *but* the 'above' vapor' is enriched in EtOH molecules and fewer H2O molecules.
>> It doesn't require 38560 - 40650 J/mol coming in from the boiler for every reflux reaction?
I think terminology is big part of this issue, so excuse my lengthy, didactic, semi-annoying reply. In my dictionary, 'reflux' is what happens at the very top of a still when you take a fraction of the condensate and run it back to the top plate. (liquid) Overflow happens from there, down to the feed point ..., as liquid dribbles downward. There is (almost) no chemical 'reaction' - and I reserve the word 'reaction' for chemical reaction.
What you are describing is "phase change", not a chemical reaction; converting gas to liquid and back; and this involves energy exchange. It happens at every plate, almost "equimolar" flow of vapor flow upward *IF* the plates are near equilibrium w/ the vapor above.
In terms of energy, vaporization (and corresponding condensation) is the 88+% explanation of all distillation energy flux. If you get your wash to 75C, then vit's 95+% of the energy flux. Yes, we need to heat wash from ambient toward the bubble point. Yes, there really is a LITTLE enthalpy of mixing. [Mixing water+EtOH (below the azeotrope) produce a little heat]. But vaporization&condensation are the main dish.
I *think* you are aiming at this true statement. If we vaporize one mol of (mostly water) molecules at the bottom/re-boiler, then we allow that vapor to condense and re-vaporize at each plate, whilst concentrating EtOH at each re-vaporization, then at the top of the still column we have one mol of (mostly) EtOH molecules without further energy introduction. Yes - that is the basis of the McCabe-Thiele method. It describes water+ethanol distillation accurately.
What you (and I, before I studied) are ignoring is that without reflux from the top, and overflow all the way down - there is no liquid on those plates! Without the liquid from above, there is no new LVE equilibrium point, and therefore no enriched EtOH. Your fancy 16 plate column become exactly one plate when run w/o reflux! No reflux = no enrichment beyond the first step; the reboiler is effectively that one plate !!!
Yes you get almost the same amt of vapor mols-out at top, as mols-in b/c the heat of vaporization is similar. PERIOD. NO - you don't get any further enrichment beyond the first vaporization UNLESS you keep the plates wet via reflux from the top, and overflow downward!! The amount of reflux needed to keep "the plates wet" is determined by the MINIMUM REFLUX RATIO calculated in a previous post and based only on the product concentration (ABV) and the feed concentration (ABV), the feed-quality (it's enthalpy vs vaporization energy) and the VLE characteristics(fixed).
Practically for neutral spirit product with a liquid ~10%ABV feed, your reflux ratio(RR) is at least 4 (for every unit of vapor condensed at top, 80% is refluxed and 20% is product (RR = 80%/20%= 4). Everything of interest has a vaporization energy ~40kJ/mol, and your RR=4 in order to keep your plates wet, so you need to vaporize 5 mols at the base to get 1 mol of product. IOW 1 mol of product costs you 200 kJ of vaporization heating energy (and another 200kJ of condensation cooling energy at the top) !
>>What actually costs energy? Heat coming off uninsulated equipment into the environment. Heat in the collected product or low ABV waste being drained if those temps are above the incoming beer temperature. Heat in any external cooling beyond using the incoming feed.
The energy FLUX of an IDEAL still considers the enthalpy of the feed, bottoms and product (which is small change, almost ignorable if all are liquid phase) and the big factors are the heating a the base for vaporization and cooling(condensation) at the head. The ideal still is insulated and loses nothing out the surface. When you reflux a fraction of the condensed vapor, that is heat energy that does not directly result in product. Instead it results in extra enrichment by creating new (loaded plate) equilibrium levels.
So perhaps you add 200kJ at 40kJ/mol to vaporize 5 mol at the bottom. The 5mol are converted along the way to be more enriched. At the top you condense this 5mol of more-EtOH vapor and send 4mol back down to wet the plates as reflux, and collect 1 mol as product. You just spent 200kJ heating (and 200kJ cooling) to obtain 1mol of product. The reflux costs a lot of energy but results in extra equilibrium stages and concentration.
>>So reflux cost energy because it reduces rate of product take off, so for the same quantity of product collect, it increases amount of time the equipment is operating hot and radiating heat losses into the environment.



Reflux costs energy b/c for every mol of reflux you must add 40kJ to vaporize it, then remove 40kJ to condense it. BUT, to get sufficient concentration from a liquid-phase 10%ABV feed, to produce neutral spirits means that you must reflux ~80% of the vapor, while collecting only 20%!. That is the expense.
Note that at lower product concentrations the reflux and energy costs drop and the column size drops. For example:
10%ABV liquid feed still, to get neutral spirits, practically your reflux ratio RR=4 or greater (and a large number of plates); 80% refluxed.
For the same 10%ABV liquid feed, to obtain white-dog whiskey around 68%ABV, 38%mol-fraction, requires a reflux ratio RR=0.84; 45% refluxed.
To produce a mol of neutral requires (4+1)*40kJ = 200kJ of heat
To produce a mol of whiskey requires a (1+0.84)*40kJ =73.6jkJ
Per mol whiskey distillation requires only 37% [73.6/200] of the energy!
The heat energy determines the mols of vapor, and this (almost) determines the rate of vapor flow up the column. The vapor flow (and temperature) rate is limited by "flooding" where the liquid and esp mist droplets from above fall 'upward' in the vapor wind.
So in the same diameter column, you can produce whiskey at about 2.7 [1/37%] times the rate as neutral spirits.
===
*** Side note on practical stills***
A 60 inch diameter, still at MGPI has relatively little energy loss through it's surface compared to the vapor energy in the volume. . A 2" diameter still radiates and loses to convection a much larger fraction of energy. Small stills should be insulated!\
Small stills made of copper shell a LOT of heat up and down the column, and across (copper) plates. This cause separation inefficiency and costs hundreds of watts in a small still. An ideal small still would have a column and plates made of decent thermal insulators (glass, ceramics) and certainly not copper. [Yes, you want some copper in the vapor section to deal with sulfur compounds].
Re: Doug's continuous distillation
I need to correct/revise/clarify that.
The energy amount isn't large at all compared to the energy used for any rectification of neutral spirits from say a 10%ABV wash.
*BUT* the heating of the feed changes the angle of the q-line in the McCabe-Thiele and that can make a huge difference in the number of plates, and even the required reflux ratio for a given problem.
[Oddly, hotter feed isn't always better. For a given reflux ratio, and fixed feed and distillate concentration, the number of plates will vary in rather odd ways as the q-line (feed quality) changes. Normally hotter is better, and certainly in terms of reducing the number of rectification plates, but it seems the stripping section *may require slightly fewer plates with cooler wash for typical beverage distilling circumstances.]
Re: Doug's continuous distillation
Football wrote:
"So reflux cost energy because it reduces rate of product take off,,,"
It also raises the abv.
You have to think in proof gallons.
And then you have to identify which "efficiency" needs to be exploited the most. Usually labor hours will be the priority.
Sorry stevea, the ability to save/recover 100,000 btu on a system that would otherwise use 600,000 btu is a significant ROI in any financial market space.
Obviously we do not at all envision the same process flow.
Steava said:
"What you (and I, before I studied) are ignoring is that without reflux from the top, and overflow all the way down - there is no liquid on those plates! Without the liquid from above, there is no new LVE equilibrium point, and therefore no enriched EtOH. Your fancy 16 plate column become exactly one plate when run w/o reflux! No reflux = no enrichment beyond the first step; the reboiler is effectively that one plate !!!"
This is just not true.
Feed beer at the 10th plate of a 10 plate beer stripper and you don't need one bit of forced reflux to enrich from 10% to 50% .
Much of the alcohol flashes early. But some alcohol does make it's way further down the column to at some point flash. This is the catalyst that enriches the beer column with no reflux notwithstanding the continuous beer feed of 10%. Ah!! The beer feed.
Less white board and more practical application please.
"So reflux cost energy because it reduces rate of product take off,,,"
It also raises the abv.
You have to think in proof gallons.
And then you have to identify which "efficiency" needs to be exploited the most. Usually labor hours will be the priority.
Sorry stevea, the ability to save/recover 100,000 btu on a system that would otherwise use 600,000 btu is a significant ROI in any financial market space.
Obviously we do not at all envision the same process flow.
Steava said:
"What you (and I, before I studied) are ignoring is that without reflux from the top, and overflow all the way down - there is no liquid on those plates! Without the liquid from above, there is no new LVE equilibrium point, and therefore no enriched EtOH. Your fancy 16 plate column become exactly one plate when run w/o reflux! No reflux = no enrichment beyond the first step; the reboiler is effectively that one plate !!!"
This is just not true.
Feed beer at the 10th plate of a 10 plate beer stripper and you don't need one bit of forced reflux to enrich from 10% to 50% .
Much of the alcohol flashes early. But some alcohol does make it's way further down the column to at some point flash. This is the catalyst that enriches the beer column with no reflux notwithstanding the continuous beer feed of 10%. Ah!! The beer feed.
Less white board and more practical application please.
Trample the injured and hurdle the dead.
Re: Doug's continuous distillation
Stevea said:
"[Oddly, hotter feed isn't always better. For a given reflux ratio, and fixed feed and distillate concentration, the number of plates will vary in rather odd ways as the q-line (feed quality) changes. Normally hotter is better, and certainly in terms of reducing the number of rectification plates, but it seems the stripping section *may require slightly fewer plates with cooler wash for typical beverage distilling circumstances.]"
Well a hotter feed will reduce the abv coming off of the stripper. That's not bad if your looking to lay down whiskey.
Fewer plates? Like how many fewer plates. What kind of plates?
What is your reasoning?
Also, when talking about a fixed feed, are we talking about a per minute basis or per hour basis. IMO, feed rates should be governed by a target temperature ( or multiples) somewhere on the system. As such, the feed rate can and does vary on a minute by minute basis.
My point being that thinking of "fixed feed rate"s is not the best way to describe a system that operates according to a target temperature. And btw, systems that operate according to target temps run very well.
"[Oddly, hotter feed isn't always better. For a given reflux ratio, and fixed feed and distillate concentration, the number of plates will vary in rather odd ways as the q-line (feed quality) changes. Normally hotter is better, and certainly in terms of reducing the number of rectification plates, but it seems the stripping section *may require slightly fewer plates with cooler wash for typical beverage distilling circumstances.]"
Well a hotter feed will reduce the abv coming off of the stripper. That's not bad if your looking to lay down whiskey.
Fewer plates? Like how many fewer plates. What kind of plates?
What is your reasoning?
Also, when talking about a fixed feed, are we talking about a per minute basis or per hour basis. IMO, feed rates should be governed by a target temperature ( or multiples) somewhere on the system. As such, the feed rate can and does vary on a minute by minute basis.
My point being that thinking of "fixed feed rate"s is not the best way to describe a system that operates according to a target temperature. And btw, systems that operate according to target temps run very well.
Trample the injured and hurdle the dead.
-
- Swill Maker
- Posts: 331
- Joined: Fri Feb 15, 2019 5:52 am
Re: Doug's continuous distillation
You can replace the forced reflux with cold feed to some point. But this doesn't change the physics that zero reflux means zero rectification.LWTCS wrote: ↑Sun Mar 20, 2022 7:43 am Feed beer at the 10th plate of a 10 plate beer stripper and you don't need one bit of forced reflux to enrich from 10% to 50% .
Much of the alcohol flashes early. But some alcohol does make it's way further down the column to at some point flash. This is the catalyst that enriches the beer column with no reflux notwithstanding the continuous beer feed of 10%. Ah!! The beer feed.
Less white board and more practical application please.
And it doesn't change the energy costs of rectification. If you don't preheat the feed you will need more steam from the bottom.
Re: Doug's continuous distillation
Yes. I believe that to be a more accurate way of explaining.Hügelwilli wrote: ↑Sun Mar 20, 2022 9:37 amYou can replace the forced reflux with cold feed to some point. But this doesn't change the physics that zero reflux means zero rectification.LWTCS wrote: ↑Sun Mar 20, 2022 7:43 am Feed beer at the 10th plate of a 10 plate beer stripper and you don't need one bit of forced reflux to enrich from 10% to 50% .
Much of the alcohol flashes early. But some alcohol does make it's way further down the column to at some point flash. This is the catalyst that enriches the beer column with no reflux notwithstanding the continuous beer feed of 10%. Ah!! The beer feed.
Less white board and more practical application please.
And it doesn't change the energy costs of rectification. If you don't preheat the feed you will need more steam from the bottom.
Trample the injured and hurdle the dead.
-
- Rumrunner
- Posts: 694
- Joined: Wed Mar 11, 2009 9:13 pm
Re: Doug's continuous distillation
Imagine a different paradigm.
What if rather than boiling ALL the water repeatedly we inject boiling beer mid point in the column so that ONLY pure water dripped off the bottom of the column into the boiler.
What reflux rate would this require?
Imagine if you run a 72 plate reflux column on top of a pot still. First we run it at 95 percen etoh. Then We run it 80 percent. Which requires more energy? The answer is the column will only take so much energy before flooding out regardless of percent at the top.
Stevea you never got back to me about latent heat of vaporization. Do you understand what that is?
Now I know how you claim azeo so easy, it's based on a meat thermometer. :lol:
-
- Rumrunner
- Posts: 694
- Joined: Wed Mar 11, 2009 9:13 pm
Re: Doug's continuous distillation
Things that consume energy in my still.football29 wrote: ↑Tue Mar 15, 2022 10:49 amThe still in this thread operates at 20 gph of 10% wash with 3800 watts, or 2000 watt hours for 1 gallon of ethanol, so 200 W-hr per gallon of wash.
There doesn't look like theres heat pumps just direct heat exchangers, and it looks like it loses heat to the environment, so its not a theoretically perfect distiller. Where could the discrepancy be![]()
Vaporization requires heat put into the device, condensation requires heat taken from the device.
Reflux is vaporization and condensation occuring together inside the still, right? It doesn't require 38560 - 40650 J/mol coming in from the boiler for every reflux reaction?
What actually costs energy? Heat coming off uninsulated equipment into the environment. Heat in the collected product or low ABV waste being drained if those temps are above the incoming beer temperature. Heat in any external cooling beyond using the incoming feed.
So reflux cost energy because it reduces rate of product take off, so for the same quantity of product collect, it increases amount of time the equipment is operating hot and radiating heat losses into the environment.![]()
![]()
![]()
1. Vaporizing etoh from the top of the column to the condenser.
2. Heat loss out the hoses and exchangers and column.
3. The out put spent wash and product are warmer than what went in.
In a pot still, you have to boil the wash over and over because the liquid coming off the column back into the boiler contains AT LEAST as much alcohol as the stuff in the boiler. So, you have to reflux 70 percent to condense the water and etoh back into the boiler.
My still is continuous. It requires enough reflux to ensure the temperature gradient so the top of the column is colder than the bottom.
Now I know how you claim azeo so easy, it's based on a meat thermometer. :lol:
-
- Rumrunner
- Posts: 694
- Joined: Wed Mar 11, 2009 9:13 pm
Re: Doug's continuous distillation
I don't know ANYTHING about flavors or taste or fusels. Just looking at making fuel.LWTCS wrote: ↑Sun Mar 20, 2022 7:43 am Football wrote:
"So reflux cost energy because it reduces rate of product take off,,,"
It also raises the abv.
You have to think in proof gallons.
And then you have to identify which "efficiency" needs to be exploited the most. Usually labor hours will be the priority.
Sorry stevea, the ability to save/recover 100,000 btu on a system that would otherwise use 600,000 btu is a significant ROI in any financial market space.
Obviously we do not at all envision the same process flow.
Steava said:
"What you (and I, before I studied) are ignoring is that without reflux from the top, and overflow all the way down - there is no liquid on those plates! Without the liquid from above, there is no new LVE equilibrium point, and therefore no enriched EtOH. Your fancy 16 plate column become exactly one plate when run w/o reflux! No reflux = no enrichment beyond the first step; the reboiler is effectively that one plate !!!"
This is just not true.
Feed beer at the 10th plate of a 10 plate beer stripper and you don't need one bit of forced reflux to enrich from 10% to 50% .
Much of the alcohol flashes early. But some alcohol does make it's way further down the column to at some point flash. This is the catalyst that enriches the beer column with no reflux notwithstanding the continuous beer feed of 10%. Ah!! The beer feed.
Less white board and more practical application please.
I don't believe more plates will cost anything. So if 30 plates is good, then 40 plates won't make less 95 percent than 30. Assuming pressures don't go up of course.
Not enough plates means a lot more reflux to reach 95 percent.
As you know I use 13 mm marbles 36 inches high on each of the stripping column and the upper column.
What are your thoughts?
Last edited by drmiller100 on Sun Mar 20, 2022 6:20 pm, edited 1 time in total.
Now I know how you claim azeo so easy, it's based on a meat thermometer. :lol:
-
- Rumrunner
- Posts: 694
- Joined: Wed Mar 11, 2009 9:13 pm
Re: Doug's continuous distillation
People in China drink a lot of tea. Neither statement has fuckall to do with distillation.
Now I know how you claim azeo so easy, it's based on a meat thermometer. :lol:
-
- Novice
- Posts: 27
- Joined: Sat Jul 18, 2020 3:58 pm
Re: Doug's continuous distillation
Any rectification column (of a given height with a given packing) needs the same reflux given mash ABV and given product ABV, whether its batch or continuous feeddrmiller100 wrote: ↑Sun Mar 20, 2022 6:10 pm My still is continuous. It requires enough reflux to ensure the temperature gradient so the top of the column is colder than the bottom.


Stevea I believe is saying it is for example 80% reflux required if you have 10% feed and taking off ~96% product. Whether or not those 10% feed vapors enter the rectification column from a big batch pot kettle or injected into the top of a stripping column below.
To take off 2 gallons of etoh per hour you must inject 20 gallons of 10% wash per hour and inject enough heat to vaporize ~100 gallons of water in the bottom boiler, and take away enough heat to reflux 80 gallons per hour at the top of the column.
A 3800w heating element in water does not vaporize that much steam.

-
- Rumrunner
- Posts: 694
- Joined: Wed Mar 11, 2009 9:13 pm
Re: Doug's continuous distillation
[quote=football29
>>To take off 2 gallons of etoh per hour you must inject 20 gallons of 10% wash per hour
Yes.
>>and inject enough heat to vaporize ~100 gallons of water in the bottom boiler,
No. Why would you say this? I have 36 inches of column BELOW where I inject the beer. This is reflux rectified so that only pure water drips into the boiler.
Also you went from 20 gallons per hour to 100 gallons total. This is not a pot still. It is continuous.
a>>nd take away enough heat to reflux 80 gallons per hour at the top of the column.
No.
>>*A 3800w heating element in water does not vaporize that much steam.
Smiles.......
If you think recursion, I only NEED enough heat to vaporize the 2gph of etoh at the top of the packing to get it up to the condenser.
Smiles.....
>>To take off 2 gallons of etoh per hour you must inject 20 gallons of 10% wash per hour
Yes.
>>and inject enough heat to vaporize ~100 gallons of water in the bottom boiler,
No. Why would you say this? I have 36 inches of column BELOW where I inject the beer. This is reflux rectified so that only pure water drips into the boiler.
Also you went from 20 gallons per hour to 100 gallons total. This is not a pot still. It is continuous.
a>>nd take away enough heat to reflux 80 gallons per hour at the top of the column.
No.
>>*A 3800w heating element in water does not vaporize that much steam.

Smiles.......
If you think recursion, I only NEED enough heat to vaporize the 2gph of etoh at the top of the packing to get it up to the condenser.
Smiles.....
Now I know how you claim azeo so easy, it's based on a meat thermometer. :lol:
-
- Novice
- Posts: 27
- Joined: Sat Jul 18, 2020 3:58 pm
Re: Doug's continuous distillation
Because Stevea told me this a few replies up, referencing his graph.
*some* amount of reflux is required, i'm not a chemical engineer, but it sounds like Stevea's information is the precise amount of reflux required to get to 95% product from 10% feed.
drmiller100 wrote: ↑Sun Mar 20, 2022 7:24 pm
Also you went from 20 gallons per hour to 100 gallons total. This is not a pot still. It is continuous.
My understanding of the theory, is that packing or plates or a very tall column all accomplish the same thing, rectification wise (but are very different in terms of clogging, cleaning, etc).stevea wrote: ↑Sun Mar 20, 2022 3:55 am Reflux costs energy b/c for every mol of reflux you must add 40kJ to vaporize it, then remove 40kJ to condense it. BUT, to get sufficient concentration from a liquid-phase 10%ABV feed, to produce neutral spirits means that you must reflux ~80% of the vapor, while collecting only 20%!. That is the expense.

Last edited by football29 on Sun Mar 20, 2022 8:27 pm, edited 1 time in total.
-
- Novice
- Posts: 27
- Joined: Sat Jul 18, 2020 3:58 pm
Re: Doug's continuous distillation
OK, maybe this is a source of confusion.drmiller100 wrote: ↑Thu Feb 17, 2022 8:08 pm We've had some disconnects. What does latent heat of vaporization mean to you?
To me it means a pound of water requires 3 times as much energy to phase change to vapor as does a pound of etoh.
To me, a gallon of water weighs about 8 pounds. A gallon. Of Etioh is about 6 pounds.
Does this seem about right to you?
Stevea talks about energy per MOLE, and the heat of vaporization per MOLE is close with water and ethanol. 43 and 40 kj/MOL
heat of vaporization kj/kg has about a factor of 3 between water and ethanol, 2260 and 980 kj/kg. https://www.engineeringtoolbox.com/flui ... d_147.html
It's not immediately clear which value should be used, but obviously there's a big (factor of 3) difference between them.
-
- Novice
- Posts: 27
- Joined: Sat Jul 18, 2020 3:58 pm
Re: Doug's continuous distillation
I want to believe
drmiller100 wrote: ↑Sun Mar 20, 2022 6:04 pm
What if rather than boiling ALL the water repeatedly we inject boiling beer mid point in the column so that ONLY pure water dripped off the bottom of the column into the boiler.
OK, BY Injecting "boiling beer", do you mean you are injecting beer vapors (GAS PHASE) into the column, rather than beer (LIQUID PHASE) at its boiling temperature.
If so, Does this vaporization of beer happen via heat exchanger with the bottoms drain?
-
- Novice
- Posts: 27
- Joined: Sat Jul 18, 2020 3:58 pm
Re: Doug's continuous distillation
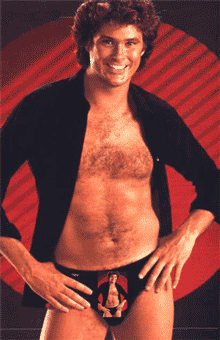
OK. THis is how I used to think about it, until Stevea educated me. I thought you could just maintain the temperature gradient and reflux happens over and over (for free) and you only put in energy to vaporize what you take out. Stevea says reflux only happens proportional to Driving vapor up the column (from the bottom boiler or steam injection) and reflux must happen 4x before you take off 1x of vapor. There is a big discrepancy in my mind.drmiller100 wrote: ↑Sun Mar 20, 2022 7:24 pm I only NEED enough heat to vaporize the 2gph of etoh at the top of the packing to get it up to the condenser.
Smiles.....
Will you reveal your design?
-
- Rumrunner
- Posts: 694
- Joined: Wed Mar 11, 2009 9:13 pm
Re: Doug's continuous distillation
Steve certainly has his own unique perspective.football29 wrote: ↑Sun Mar 20, 2022 9:26 pm
OK. THis is how I used to think about it, until Stevea educated me. I thought you could just maintain the temperature gradient and reflux happens over and over (for free) and you only put in energy to vaporize what you take out. Stevea says reflux only happens proportional to Driving vapor up the column (from the bottom boiler or steam injection) and reflux must happen 4x before you take off 1x of vapor. There is a big discrepancy in my mind.drmiller100 wrote: ↑Sun Mar 20, 2022 7:24 pm I only NEED enough heat to vaporize the 2gph of etoh at the top of the packing to get it up to the condenser.
Smiles.....
Will you reveal your design?
I thought I had revealed my design???
Now I know how you claim azeo so easy, it's based on a meat thermometer. :lol:
-
- Rumrunner
- Posts: 694
- Joined: Wed Mar 11, 2009 9:13 pm
Re: Doug's continuous distillation
football29 wrote: ↑Sun Mar 20, 2022 8:55 pmI want to believedrmiller100 wrote: ↑Sun Mar 20, 2022 6:04 pm
What if rather than boiling ALL the water repeatedly we inject boiling beer mid point in the column so that ONLY pure water dripped off the bottom of the column into the boiler.
OK, BY Injecting "boiling beer", do you mean you are injecting beer vapors (GAS PHASE) into the column, rather than beer (LIQUID PHASE) at its boiling temperature.
If so, Does this vaporization of beer happen via heat exchanger with the bottoms drain?
When things are going really well the beer is starting to percolate as it goes through final heat exchange just before going into column.
Now I know how you claim azeo so easy, it's based on a meat thermometer. :lol:
-
- Novice
- Posts: 27
- Joined: Sat Jul 18, 2020 3:58 pm
Re: Doug's continuous distillation
I've read most of your post history and seen design elements but not a complete design.
Your column is slanted rather than vertical.
You use marbles for packing.
You use a needle valve somewhere

You have an electric heating element in the bottom boiler waste fluid , go generate rising steam in the column

Do you use external cooling water, for either reflux condensor and/or product condensor? Or do you use incoming feed to condense?
Where else do you get your improved efficiency from?
Re: Doug's continuous distillation
*IF* you want higher ABV product off a column, then you *MUST* add energy via reflux to separate against entropy - NO EXCEPTION.LWTCS wrote: ↑Sun Mar 20, 2022 7:43 am Football wrote:
"So reflux cost energy because it reduces rate of product take off,,,"
It also raises the abv.
You have to think in proof gallons.
And then you have to identify which "efficiency" needs to be exploited the most. Usually labor hours will be the priority.
*IF* you want optimal proof-gallons (the most ethanol) - then you should learn to drink 10% ABV grist-y wash. {no one rational does that}.
We agree that labor is a huge factor in the trade-offs. OTOH I doubt that running a borosilicate tube and ceramic plate column takes any more labor and should have considerably higher throughput, lower height and operate at lower power.
I think you misread my intentions. The OPs claim about energy efficiency flies in the face of all known ChemE practice - by a large factor. It's extremely likely to be wrong. And I certainly OUTLINED the lower limits of energy reqs for ANY distillation based only on fundamental theory.Sorry stevea, the ability to save/recover 100,000 btu on a system that would otherwise use 600,000 btu is a significant ROI in any financial market space.
Obviously we do not at all envision the same process flow.
This isn't about saving every last cent on energy - its about understanding the factual limits, AND understanding HOW to create efficient distillation. If you have a GOOD REASON to squander energy for some greater cause - especially flavor quality - then I am very interested. If you want to squander energy b/c you don't understand the design parameters, then you are just acting from ignorance or tradition. I strongly suspect you'll need about double the energy and perhaps 50% more practical plates. That sounds 'not smart' unless you get something good in return.
We agree that the theoretical heat add is about 0.5 kW-hour per gallon of feed. That's about 6 cents per gallon of feed for electric ENERGY in my area. If inefficiency doubles or triples that ENERGY cost, it's still a "don't care" price item. The bigger problem is the instantaneous POWER (energy per unit time) and cooling and the number of plates. If you can cut your power needs in half and make a still 30% shorter, that's a win.
My main point is that until we understand how distillation "works" and what is optimal, we have no basis to evaluate trade-offs. I'd like to understand what is near-optimal, and then make JUDICIOUS trade-offs from there.
Yes it is true. Examine the McCabe-T diagram posted above. Find 10% ABV = 0.032 mol fraction on the X-axis, then go UP and see this intersects the VLE curve at 0.25mf on the Y-axis; and 0.25mf = 53% ABV. What you have described (10%ABV liquid to 50% ABV vapor) IS one plate of separation - just as I said.... This is just not true.
Feed beer at the 10th plate of a 10 plate beer stripper and you don't need one bit of forced reflux to enrich from 10% to 50% .
Stripper comment:
I really don't get your terminology, nor explanation. 'FLASH' distillation is a very real thing (involves lowering pressure to instantaneously boil-off a fraction of feed) , but definitely NOT happening here, nor in an isobaric(common) still, Your 'point flash' means little to me - explain.Much of the alcohol flashes early. But some alcohol does make it's way further down the column to at some point flash. This is the catalyst that enriches the beer column with no reflux notwithstanding the continuous beer feed of 10%. Ah!! The beer feed.
In a stripper your plates are operating between the VLE curve and the "stripping operating line" which is actually pretty easy to derive from theory as a straight line on a McCabe-T diagram.
In an isolated stripper (no overflow from rectification, which changes the op-line), with feed near it's boiling point, it takes a very large number of plates to get product vapor that is fully "one plate better" than the feed (say 10%ABV to 53% ABV). however you can get very close with a modest number of plates.
My description would be that the feed at the top plate absorbs high enthalpy, lower ABV vapor from below and this causes an exchange the released higher ABV vapor product. The next plate down loads with partially depleted overflow wash from above, and it too absorbs higher enthalpy, lower ABV vapor from below and ... I've a McCabe-Thiele spreadsheet, and I converted the values to ABV% so in such a stripper we see ...
Code: Select all
plate AVB.liq ABV.vap
1 9.97% 52.31%
2 8.58% 50.27%
3 7.71% 47.34%
4 6.22% 43.05%
5 4.71% 36.67%
6 3.48% 29.06%
7 2.23% 20.43%
8 1.28% 12.56%
9 0.64% 6.52%
10 0.13% 1.28%
The MOST effective plates on a molar basis are plates 3,4,5, NOT the top plate as you seem to have suggested.
The explanation is clear if you examine a McCabe-T with a stripper operating line drawn in. The bottom plates don't vaporize a lot of mols of EtOH b/c the wash is too depleted and low ABV at the bottom. The top plates also don't extract as many mols of EtOH b/c the vapor from below is already near the VLE limit. IOW The 50.27%ABV vapor from plate2 can't do very much depletion from a 10%ABV feed at plate1, which has a VLE limit of 53%ABV.
BTW - it's true that you can add more stripping plates and lose less EtOH at the bottom at essentially no energy cost. I think I misunderstood the calculation in Miller's "Whisky Science ..' book.
If we don't understand this very-basic white-board (theory), then we CAN'T understand the concepts, and we CAN'T see the obvious truths & errors. You made two gaffes here. You didn't see that 10%ABV=>50%ABV vapor is one theoretical separation plate; that's about reading a VLE curve. You didn't (seem to) see that the effectiveness of plates (stripper or rectification) is related, in a McCabe-T to the vertical height of the stair-steps AND that those steps become small when constrained by the stripper operating line. Only in the past few months after manually constructing some McCabe-T diagrams did the huge importance of the q-line, and the two operating lines dawn on me. It incidentally explains the energy needed to drive a continuous still, and the peculiar issue of minimum required reflux to get a target separation.Less white board and more practical application please.
Distillation involves the application of ENERGY to reverse (locally) ENTROPY, so it's intrinsically a strange, complex beast. I don't think I'm competent to design a good practical still until I understand how it actually works. Monkey-see, monkey-do isn't a design process, and it gives you zero insight into how to make improvements.
I WILL get around to a practical design once I puzzle-out how to make effective stripper plates that can tolerate some yeast and maybe grist.
Re: Doug's continuous distillation
Ugh - I really don't want to go down the path of ancient units. Firkins of feed per fortnight using boiler-horsepower of steam is a true units nightmare.drmiller100 wrote: ↑Thu Feb 17, 2022 8:08 pm
We've had some disconnects. What does latent heat of vaporization mean to you?
To me it means a pound of water requires 3 times as much energy to phase change to vapor as does a pound of etoh.
To me, a gallon of water weighs about 8 pounds. A gallon. Of Etioh is about 6 pounds.
Does this seem about right to you?
I'll carry on in SI units and convert to your lingo along the way.
Basics:
All physical chemistry considers a mol (or sometimes mole) which is simply Avogadro's number of molecules (6.022*10^23).
A mol of carbon-12 is defined as 12 grams and this defines Avogadro's number.
A mol of water (H2O) weighs 18.01528 grams, and this is called it's "molecular weight". The mol of water at 20C(68F) has a density 0.99823 g/ml, so it's volume is 18.047224 ml.
A liter of water @20C weighs 0.99823kg (2.200 lb) and contains 55.4 mols.
A pint of water @20C weighs 1.04lbs and contains 26.2 mols.
A mol of pure, anhydrous ethanol (EtOH), weighs 46.07 grams, has density at 20C of 0.7892 g/mL, so a mol @20C has a volume of 58.376 ml.
A liter of anhydrous EOH @20C weighs 0.78923kg( 1.74lb) and contains 17.130 mols
A pint of anhydrous EOH @20C weighs 0.8233 lbs and contains 8.106 mols.
Enthalpy of vaporization (aka Heat of vaporization, aka latent heat of vaporization) is defined as the energy necessary to convert a quantity (often a mol) of liquid into vapor isothermally (no temperature change, therefore enthalpy or latent). Other quantities, mols, grams, pounds are often used, but molar enthalpy of vaporization is very common.
Water Hvap = 40660 Joules/mol (0.284 kWatt hour / pound) at 1 atmosphere.
EtOH Hvap = 38600 Joule/mol (0.106 kW hr/lb) at 1 atm.
Note that the density of both liquids decrease as they get hotter ; and the Hvap values decrease a little at higher pressure.
It's useful to know that MANY MANY liquids have a similar molar Hvap a little below water-Hvap, or around 30 to 40kJ/mol. In fact many calculation methods in distillation, even petrol cracking, rely of this fact. It means that in an ideal still at operating equilibrium, that if you introduce 1 mol of steam at the bottom you will get very nearly 1 mol of light-key+water mix out of the top. If you have interest in the theory of how distillation works you'll want to think in term of mols and molar-Hvap.
===
>>To me it means a pound of water requires 3 times as much energy to phase change to vapor as does a pound of etoh.
H2O: (40660 Joules/mol) / (18.01528g/mol) = 2256 J/gram
EtOH: (38600 J/mol) / (46.07 g/mol) = 837.85 J/gram
So water requires 2.69 times more energy PER GRAM to vaporize as compared to EtOH (same factor per pound) The molar-Hvap of water is ~5% higher. Note that the molecular weight ratio MW.etoh/MW.h20 = 2.56; a similar number to 2.69 for obvious reasons.
I can't imagine why anyone want's to consider pounds or grams of these as a reference. It seems impractical in practice and awkward in theory.